Built on standard production chassis, Yale robotic lift trucks allow you to automate repetitive, low value added tasks by picking up, transporting and dropping off pallets independently and reliably. Enhance labor productivity, optimize workflow and help increase your bottom line by transforming to robotic lift. For forklift batteries and solar battery systems. To make your new or existing forklift battery virtually maintenance free, we recommend installing an automatic battery watering system and water level indicator light. This can be accomplished for less than.
The Forklift Transmission is a crucial part that enables the movement of the forklift. It is a component of the engine assembly which connects both the engine and the wheels, allowing them to rotate in sync with each other. When the engine operates at varying ranges of revolutions per minute (RPM), transmission provides the conformity between the engine rotation and the wheel rotation, keeping them in balance. The main job of a transmission system, whether manual or automatic, is to let the engine operate at narrow ranges of speed while at the same time providing a wider range of output speeds.
A transmission system essentially is of two types, manual transmission system and automatic transmission system. Despite the fact that many old vintage Forklift trucks have been operating on manual transmission systems, modern trucks usually rely on an automatic transmission, which adds up to the ease of operators and reduces the risk of any mishandling of materials. Where previously the operator of a forklift truck used to decide in which gear he should move the truck, an automatic transmission system had freed him/her off the worry. The primary visible difference between a manual and automatic transmission is an absence of clutch and a gear shift. The gear knob when put in drive performs all the operations of a manual transmission in an amazing way, all by itself. An automatic transmission, along with its torque converter, performs the same actions as a manual transmission coupled with the clutch.
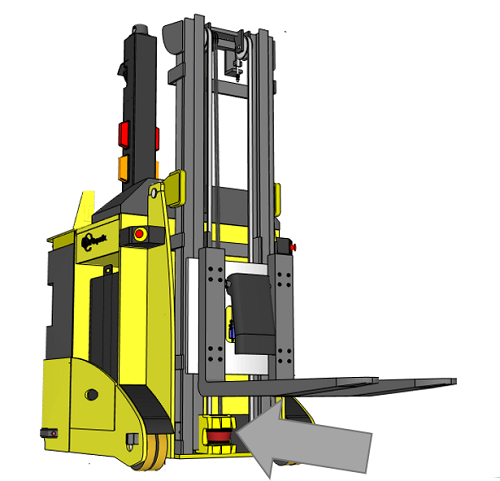
Where previously the operator of a forklift truck used to decide in which gear he should move the truck, an automatic transmission system had freed him/her off the worry. The primary visible difference between a manual and automatic transmission is an absence of clutch and a gear shift. IDEAL MSC-18K-X Mobile Column Lift, 4-Column Set, 72,000 lbs. ALI Certified w/PU Model# MSC-18K-X-472 $ 32,999 99 $ 32,999 99. Auto lift portable car lift quick jack quick jack car lift 4 post car lift car lifts lifting blocks car lifts. How doers get more done.
Forklift transmissions are made up of various components; the planetary gear set, torque converter and computer sensors. The planetary gear set allows the forklift to shift gears, allowing it to move forward and reverse. In contrast with a manual system where different gear sets are locked and unlocked at different times for obtaining varying gear ratios, an automatic transmission system uses the same set of gears called planetary gear system to produce all the various gear ratios.
As the name suggests, the gears work like the planetary solar system, in that they are configured with the largest gear in the center with varying number of smaller gears rotating around it in an orbit-like fashion. It is almost the same size as a cantaloupe and is the only part responsible for creating all of the gear ratios which transmission can produce. All other parts facilitate the planetary gear set. A planetary gears system has three parts, the sun gear, the planet gears and the ring gear. Each of the components serve different roles at different times, any of them can be input, output or may remain stationary. The gear system is complete with input and output shafts for manual transmission forklifts.
Torque converter, a replacement of clutch in annual transmission systems, keeps the engine running despite the forklift being stationary. They are found in automatic transmissions and are composed of three parts: the stator, the pump, and the turbine. A torque converter is an example of fluid coupling, which lets the engine spin more or less independent of the transmission. This can be experienced when an automatic transmission forklift is made to halt near an obstacle, the torque converter provides less torque for engine and the forklift keeps creeping. A little pressure applied on the brake pedal is necessary to put the truck to a complete stop. The housing of torque converter is attached to engine flywheel with the help of bolts, allowing it to turn at a speed similar to that of the engine. The pump of a torque converter is one type of a centrifugal pump, which flings out the fluid with its spin. This fluid enters the turbine which is already connected to the transmission, causing it to spin and move the forklift truck.
Stator is present in the center of the torque converter. It redirects the fluid coming back from turbine before it contacts the pump again. If the fluid is not stopped and is allowed to hit the pump, the engine will slow down and the power will go waste. This helps increasing the efficiency of torque in a big way. The redirection of fluid in an opposite direction is due to the way stator blades/ fins are designed. Stator has a clutch inside it, which only allows it to spin one-way, i.e in the direction opposite to the flow of fluid. During motion, transmission fluid is forced into the stator, through the turbine, by the pressure from the pump. When the forklift is not mobile, the turbine would slow down because less fluid enters. Then, the stator would get locked until the turbine speed returns. Computer sensors monitor the forklift speed, engine load, pedal position, etc. to conduct the process of gear shifting.
Over time and extensive use, transmissions can be problematic. There are various indications of a transmission that needs either to be repaired or replaced.
- For manual transmission forklifts, if the gear does not shift or is very “sticky”, the transmission is having issues. Common causes are low levels of transmission fluids, shift cable, weak clutch linkage, or the use of a wrong transmission fluid.
- Burning smell or smoke puffing from the transmission indicates that either the transmission is overheating, the transmission fluid is deficient, leaking or is dirty and requires changing.
- While the forklift is in neutral and lots of noises can be heard, the components of the transmission may need replacement. The mechanical parts may be worn down.
Forklift transmission is an essential component of the forklift’s drivability. If the transmission is having issues, it should be checked immediately by a professional mechanic. Some issues can be easy to fix such as transmission fluid leaks or lack of fluid. On the other hand, many issues are irreparable, requiring a replacement part. Solid Lift Parts Inc. provides transmission parts for a wide array of forklift makes and models. We also have remanufactured and rebuilt transmission parts available. Contact your parts specialist today for your forklift transmission parts!
Forklift Transmission Photos
Robotic forklifts and other automated warehouse solutions
Automated Guided Vehicles and Robotic Forklifts are changing the way manufacturing facilities and distribution centers view efficiency. These vehicles are a great solution for repetitive tasks, high traffic areas, and places where there is a high-risk for product damage. Toyota provides assistance to help you customize decisions about navigation methods, path selection, traffic control options, and system controls. Enabling your business to get more done while saving time and money.
- Vision Guided Vehicles (VGV): These use 3D modeling to build a map of your facility and operate effectively in it. This process can easily be integrated into your existing infrastructure and requires no wire guidance system.
- Wire, RFID, and Tape AGVs:These wire-guided and similar driverless vehicles follow a specified path generally built into or taped to the floor of the facility.
- Laser AGVs:Laser AGVs respond to multiple fixed points identified by mounted or integrated laser technology, allowing for a more flexible integration than Wire AGVs.
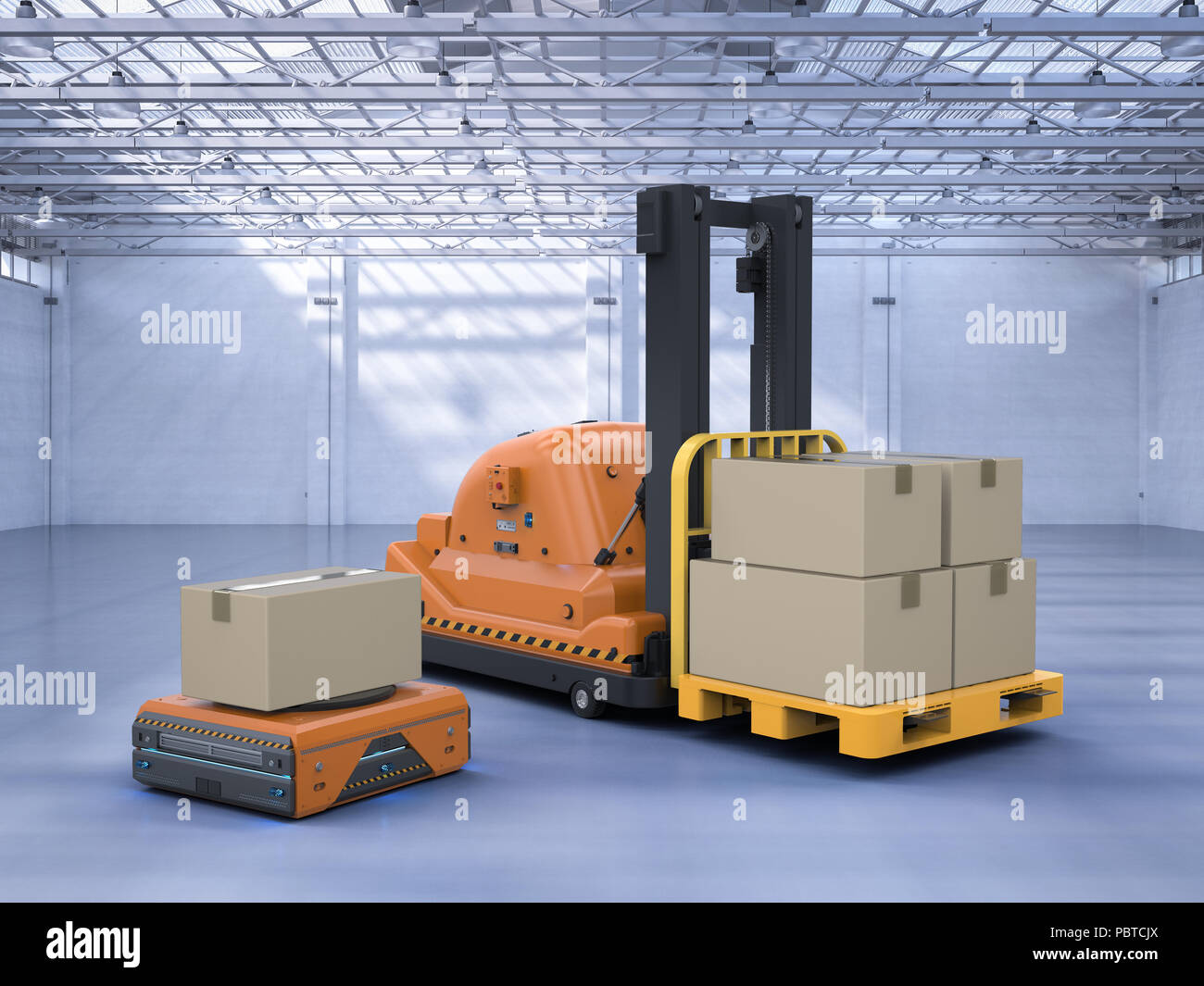
The Toyota 8HBC40A Pallet Truck is changing the way warehouses operate efficiently. This autonomous vehicle is designed to improve throughput and give their owners a dramatic competitive advantage.
- 8,000 lb. Load Capacity
- 24v AC Drive System
- Lidar-Based Navigation
- Obstacle Detection Sensors
- Wireless Connectivity
- Up to 5 MPH Travel Speed
- Full Manual Operated Mode
The Toyota 8TB50A is a robust automated towing solution. These tow tractors use cutting edge technology to safely transport 10,000 pounds without the need of an operator.
- 10,000 lb. Towing Capacity
- 24v AC Drive System
- Lidar-Based Navigation
- Manual Mode Button
- 4 MPH Travel Speed
The Toyota Mouse is efficient, dependable, and versatile. It’s a cost-effective way to optimize your manufacturing and assembly line processes through automation. The line of automated carts is ready to transport everything from raw materials to full assemblies that will connect islands of the production with ease.
- Low-Profile
- Up to 4,400 lbs. Tow Capacity
- 15 Programable Speed Settings
- 24-Volt DC Brushless Motors
- Actuated Tow Pin With Spring
- Magnetic Tape Guidance
- Laser Obstacle Scanner
- Multiple Routes on Demand
- Automatic Battery Charging Option
- On-Board Touchscreen Display
The Toyota 3AS1T Mole is a small but mighty automated guided cart that is ready to handle repeatable tasks and connect your facilities. The Mole will bring your facility on-time station delivery of raw material or products to boost productivity.
- Low-Profile
- 881 lb. Tow Capacity
- 15 Programable Speed Settings
- 24-Volt DC Brushless Motors
- Actuated Tow Pin With Spring
- Magnetic Tape Guidance
- Laser Obstacle Scanner
- Multiple Routes on Demand
- Automatic Battery Charging Option
- On-Board Touchscreen Display
Toyota Material Handling and Bastian Solutions have partnered so we are able to offer you the best material handling systems integration possible. This is a partnership that is design to support our customers in a new era of material handling
Automatic Forklift Company
Shop Warehouse Automation Solution
Automated Forklift Robot
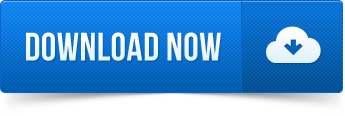